Blow molding:The process follows the basic steps found in glass blowing. A parison (heated plastic mass, generally a tube) is inflated by
air. The
air pushes the plastic against the mold to form the desired shape. Once cooled, the plastic is ejected.
The blow molding process is designed to manufacture high volume, one-piece
hollow objects. If you need to make lots of bottles, this is the process for you. Blow molding creates very uniform, thin walled containers. And, it can do so very economically.
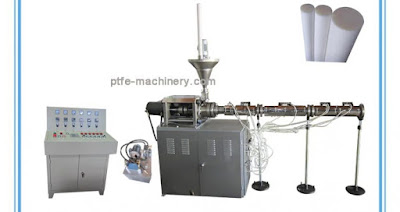
Compression molding:The name of this molding method says everything. A heated plastic material is placed in a heated mold and is then compressed into shape. The plastic can be in bulk but often comes in sheets. The heating process, called curing, insures the final part will maintain its integrity. As with other molding methods, once the part has been shaped, it is then removed from the mold. If sheeting plastic material is used, the material is first trimmed in the mold before the part is removed.
This method of molding is very suitable to high-strength compounds like thermosetting resins as well as fiberglass and reinforced
plastics. The superior strength properties of the materials used in compression molding make it an invaluable process for the automotive industry.
Extrusion molding:While other forms of molding uses
extrusion to get the plastic resins into a mold, this process extrudes the melted plastic directly into a die. The die shape, not a mold, determines the shape of the final product. The extruded “tubing” is cooled and can be cut or rolled for shipment.
Injection molding:Injection molding is by far the most versatile of all injection molding techniques. The presses used in this process vary in size and are rated based on pressure or tonnage. Larger machines can injection mold car parts. Smaller machines can produce very precise plastic parts for surgical applications. In addition, there are many types of plastic resins and additives that can be used in the injection molding process, increasing its flexibility for designers and engineers.
The process itself is fairly straightforward; however, there are many enhancements and customization techniques that can be used to produce the desired finish and structure. Injection molds, which are usually made from steel, contain cavities that will form the parts. Melted plastic is injected into the mold, filling the cavities. The mold is cooled, and the parts are ejected by pins. This process is similar to a jello mold which is filled then cooled to create the final product.
The mold making costs in this method are relatively high; however, the cost per part is very economical. Low part cost along with resin and finish options have all contributed to injection molding’s popularity in today’s manufacturing landscape.
Rotational molding:This process uses high temperatures and rotational movement to coat the inside of the mold and form the part. The constant rotation of the mold creates centrifugal force forming even-walled products. Because it is ideally suited to large
hollow containers, such as tanks, it is not a fast moving process. However, it is a very economical process for particular applications and can be cheaper than other types of molding. Very little material is wasted using this process, and excess material can often be re-used, making it an economical and environmentally viable manufacturing process.
Source: